
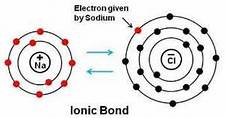
Īdhesive bonding on glass is performed through an interaction with the non bridging oxygen (NBO) e.g. The glass is then transferred to the automotive manufacturer with a risk of contamination during transport and handling. To improve the bonding between the glass and adhesive a primer with long open time is applied at the glass manufacturer. The bonding is performed on either the ceramic frit surface or the naked tin or fire side of the glass. When bonded they are compressed to a thickness of approximately 6 mm. Some contain silane as adhesion promoter and they are applied in thick triangular beads. The adhesives are flexible moisture curing adhesives that consists of binder, plasticizer, filler, carbon black, additives and catalysts. Therefore, glass bonding in automotive manufacturing is often performed with a 1C PUR adhesive.
#ION BONDING GLASS WINDOWS#
Since the glass and body in white have a difference in coefficient of thermal expansion and the windows are wide there is a need of a flexible adhesives. Today, they play a multifunctional role also acting as a stability component in the vehicle. The function of the windows in a modern car is different from the one when the windows solely were used for protection against wind and rain.
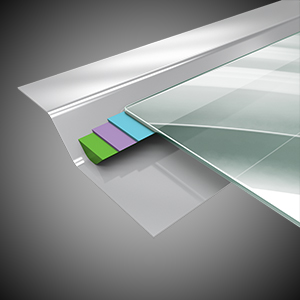
The ceramic frit is nowadays typically a zinc- or bismuth-based paint rather than a lead-based paint. The ceramic frit is used both for cosmetic and protective purposes where it is used to protect the adhesive against harmful UV rays responsible for degradation. It is fused permanently to the glass surface in a high temperature process.
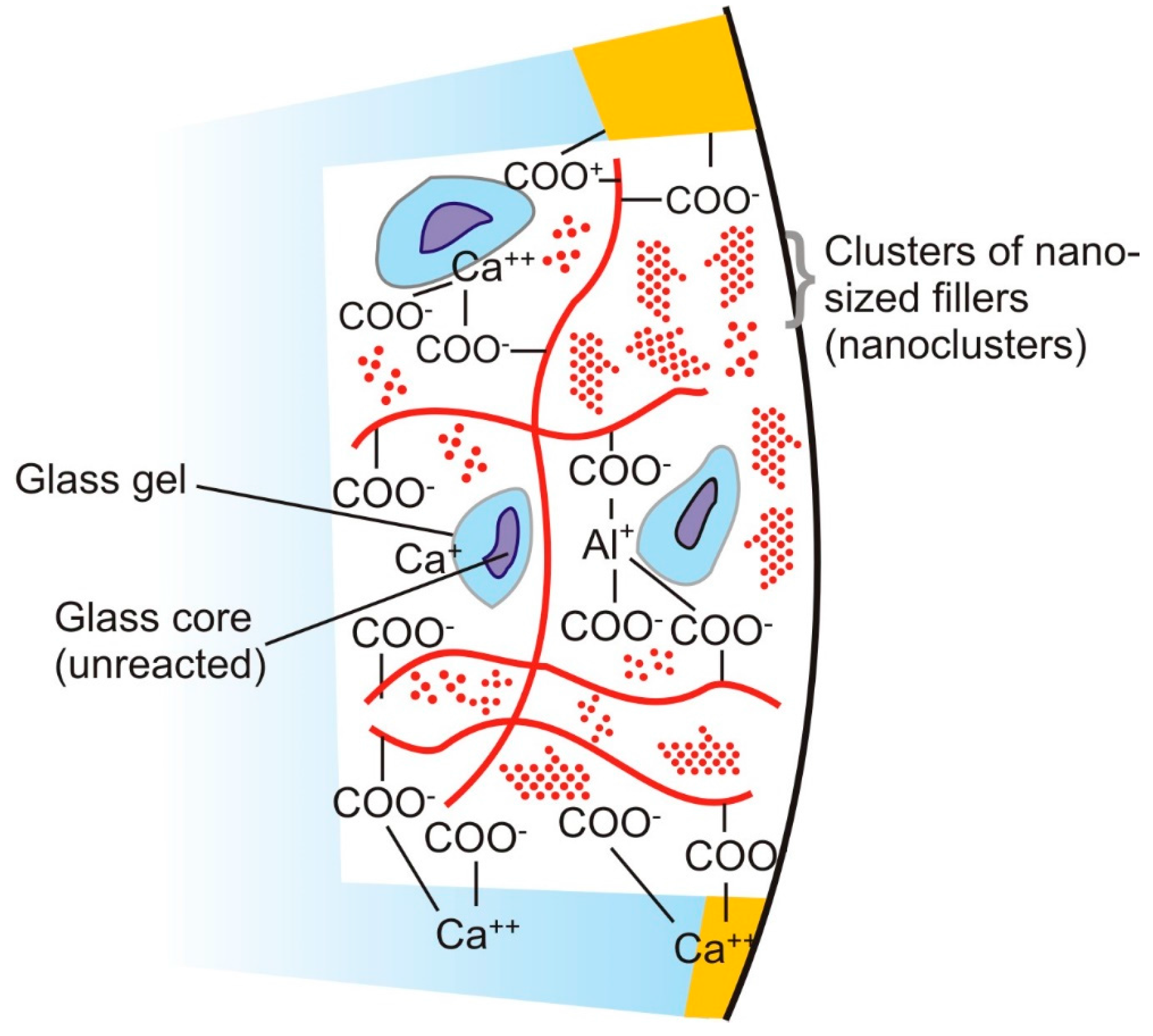
On automotive glass a pigmented glass enamel “ceramic frit” is sometimes applied to the perimeter of the windshield glass. The difference in chemistry does also affect the chemistry of the glass surfaces that will differ from each other as well as the bulk. One side will be affected from tin “tin side” and the other from the atmosphere “fire side”. From the process the glass sides will be exposed to different chemistry. In this process the surrounding atmosphere is carefully controlled with a N 2/H 2 mix that prevents oxidation of the tin bath. This result in a very flat and parallel glass. The name float glass comes from the manufacturing process were molten glass is floated out and formed on a bath usually of molten tin. In the automotive industry float glass of soda lime glass is used for different types of automotive glass. The results show that the APPT with water does not lower the level of non bridging oxygen and the bonding was further improved. A modified APPT treatment with deionized water as precursor was used. A further reaction was seen when measured after a 550 ☌ heating. A reduction in non bridging oxygen was also seen during heating of the reference glass at 100 ☌. The highest measured spot temperature of the glass during APPT was measured up to 270 ☌, but the temperature was depending on process parameters. The results show that APPT treatment can clean the surface, improve the wetting, improve the bonding but reduce the number of non bridging oxygen for the adhesive to bond to. Characterization of the glass surface was performed with surface energy through contact angle, XPS, TOF-SIMS and adhesive peel bead test. The aim of this research was to replace the chemistry of the primer with an atmospheric pressure plasma treatment (APPT) with compressed air for cleaning and activation directly before bonding. Learn more about the Ion-Exchange Process.Bonding of automotive glass is generally performed with 1C PUR adhesive on a primed ceramic frit or naked glass surface. Watch mind-bending demonstrations in The Glass Age, Part 2: Strong, Durable Glass video. Their deep understanding of the physics of glass surfaces - including diffusion, compression, tension, and resistance - are likely to yield even more remarkably tough glasses in the future. Glass scientists are constantly stress-testing glass and improving both compositions and chemical strengthening processes like ion exchange. Some advanced glasses have special compositions that help mitigate this possibility - but it’s the super-tough surface created by the ion exchange process that provide the first line of defense against everyday hazards.
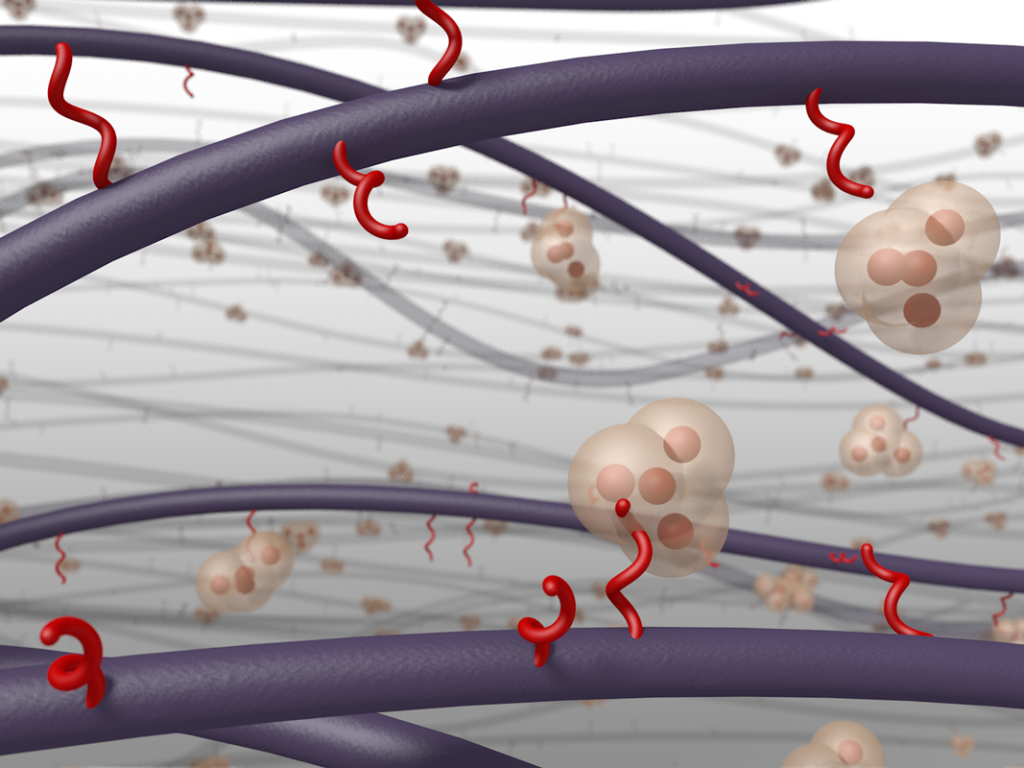
The glass retains more of its strength even after a minor nick or scratch, protecting it from more cracks and flaws. In the case of chemically strengthened glass, it’s the surface toughness that makes it ideally suited for touchscreens, appliances, and other heavy-use applications. Its surface, in effect, has become stronger through the compression of the tennis balls.
